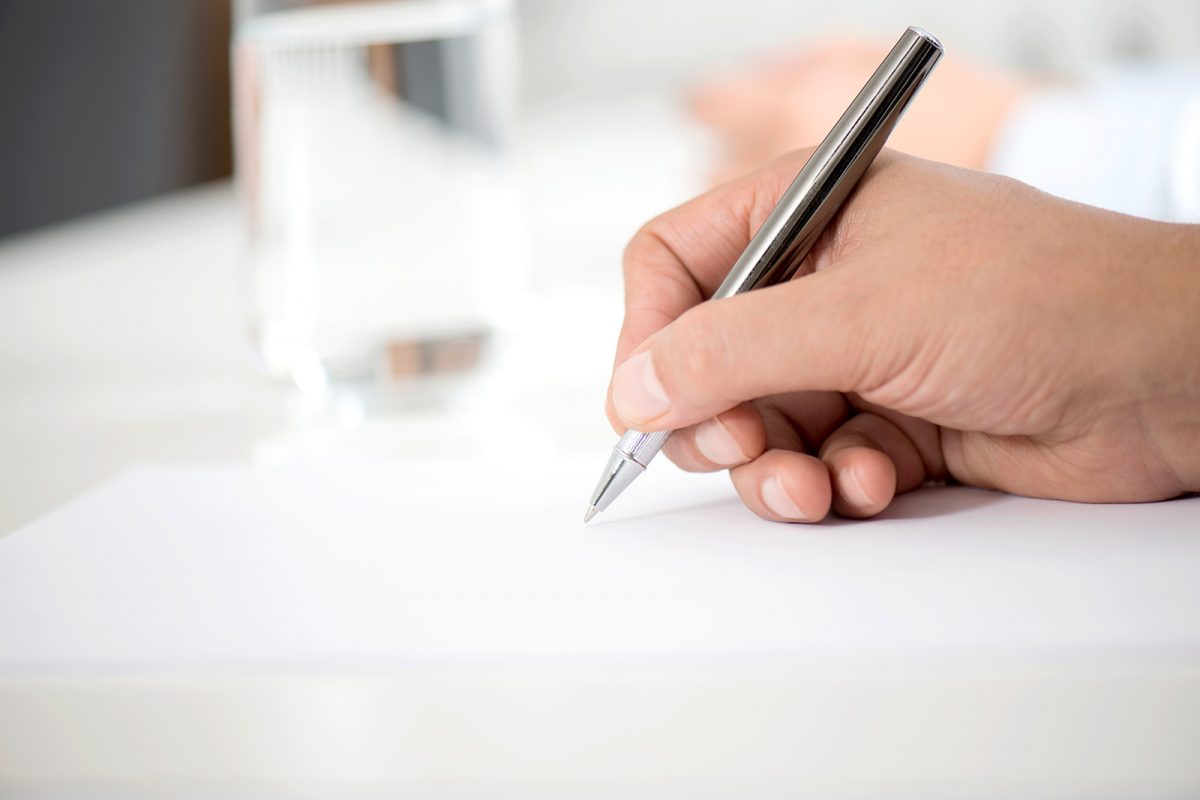
Oct 21, 2022
Battery materials making headlines in the US and in Europe
On Wednesday, the US government announced that it will award grants from the Bipartisan Infrastructure Law worth a total of US$2.8 billion to 20 manufacturing and processing companies in order to support and develop the domestic manufacturing of batteries for electric vehicles (EVs) and the electric grid.
The funding for the selected projects will support:
- Developing enough battery-grade lithium to supply approximately 2 million EVs annually,
- Developing enough battery-grade graphite to supply approximately 2 million EVs annually,
- Producing enough battery-grade nickel to supply approximately 400,000 EVs annually,
- Installing the first large-scale, commercial lithium electrolyte salt (LiPF6) production facility in the United States,
- Developing an electrode binder facility capable of supplying 45% of the anticipated domestic demand for binders for EV batteries in 2030,
- Creating the first commercial scale domestic silicon oxide production facilities to supply anode materials for an estimated 600,000 EV batteries annually,
- Installing the first lithium iron phosphate cathode facility in the United States.
When combining the Bipartisan Infrastructure Law with the measures proposed in the CHIPS & Science Act and that Inflation Reduction Act signed into law by President Joe Biden on August 16, 2022, more than $135 billion will be invested by the US to build America’s electric vehicle future, including critical minerals sourcing and processing and battery manufacturing.
On October 20th, President Biden also announced the American Battery Materials Initiative, a new effort to mobilize the entire government in securing a reliable and sustainable supply of critical minerals used for power, electricity, and electric vehicles (EVs). It will align and leverage federal resources for growing the end-to-end battery supply chain and work with private and public sector organisations, unions, different communities and governments abroad to develop more sustainable, secure, resilient supply chains. Additionally, this will support faster and fairer permitting for projects that build the domestic supply chain.
With such substantial measures, the US is catching up fast on securing the supply chain for their growing battery industry. It is therefore encouraging to see several promising battery material production projects taking place in Europa as well.
Last month, Umicore inaugurated Europe’s first “cathode Gigafactory” in Nysa, Poland. The production facility for cathode active materials is carbon neutral and an important step in achieving EU’s ambition of having its own battery ecosystem that is both sustainable and competitive on a global scale. With the establishment of its factory in Nysa, Umicore is the first company in Europe with a complete circular and sustainable battery materials value chain.
Some more promising news for minimizing Europe’s dependency on battery materials comes from Norway where Vianode, a company owned by Elkem, Hydro and Altor, has decided to invest NOK 2 billion in its first industrial-scale plant for sustainable battery materials. The industrial plant at Herøya, Norway, will produce anode graphite for about 20,000 electric vehicles (EVs) per year by 2024. This is good news as the European battery industry is highly dependant on China for their supply of graphite and anode. Apart from diversifying the anode supply chain, this projects also has strong environmental benefits, well aligned with the increasing expectations on sustainability. The graphite materials from Vianode are produced with up to 90% lower CO2 emissions than today’s standard materials.
Europe’s refining capacity is also advancing with Rock Tech concluding a €15Bn deal with Mercedes-Benz. The parties have indeed entered into a five-year term supply agreement for an average of 10,000 tonnes of battery-grade lithium hydroxide per year. This agreement represents over 40 % of the expected annual production from the planned converter capacity in Guben, Germany.
More EBA250 news
InnoEnergy, the driving force behind the EBA250 initiative, introduces today its new brand identity,…
The new EU-funded facility will enhance global raw materials partnerships and access to Critical…
Last week, InnoEnergy and EBA250 represented the battery value chain in Brussels alongside Verkor…
ElevenEs, a European LFP lithium-ion battery manufacturer, has signed a Joint Development Agreement with…
The European battery industry has come a long way since the launch of the…
The 2024 Innovation Fund calls for proposals have been launched this week, with a…
Altris, a pioneering Swedish developer of sodium-ion battery technology, has reached significant milestones that…
Last Friday, Morrow Batteries officially inaugurated the first giga-scale LFP (Lithium Iron Phosphate) cell…
On May 24, 2024, the 8th High-Level Meeting of the European Battery Alliance (EBA)…
Following the recent announcement from EVP Šefčovič on the need to support manufacturing of…