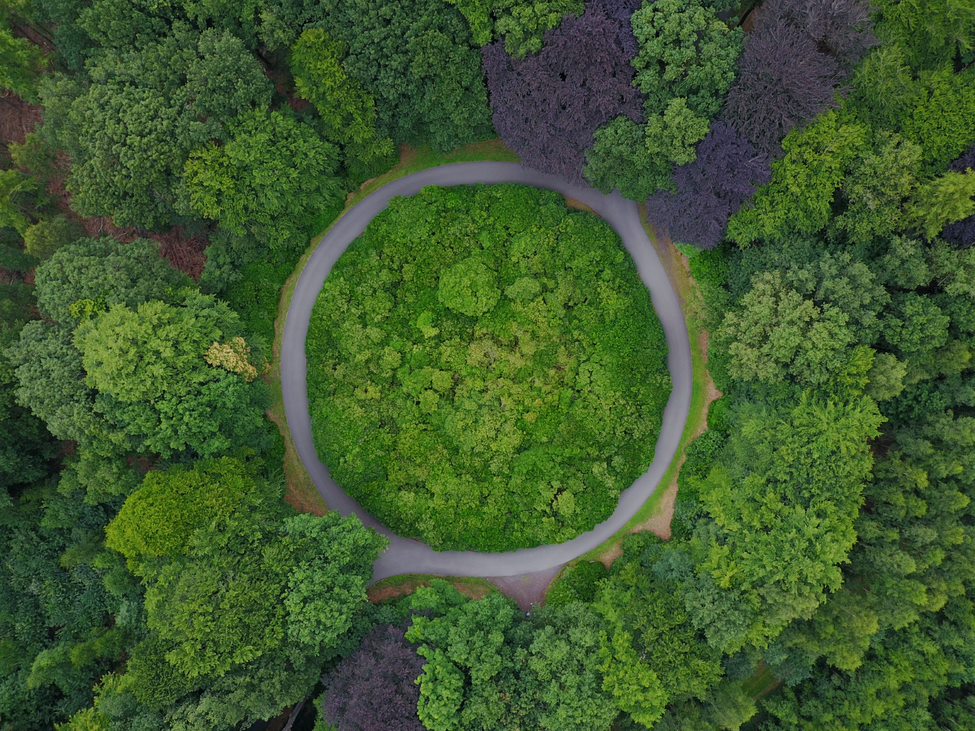
Dec 9, 2022
The sustainable future of batteries in Europe rests on a developed recycling industry
The energy transition requires a massive deployment of batteries for energy storage solutions – allowing the increase of renewables in the electricity mix – and also for electric mobility.
For electric vehicles (EVs) alone, globally there are a total of 16.5 million on the road and nearly 10% of global car sales last year were EVs. These figures have been multiplying exponentially year-on-year sending signals of a soaring battery demand for the future. To develop and accelerate the European battery industry, the European Battery Alliance, led by EIT InnoEnergy, has been working since 2017 on the gaps that need to be addressed for a fully circular, sustainable, and stable battery market, including access to raw materials and to a skilled workforce. The final and equally critical piece of the puzzle is battery recycling. In fact, a robust battery recycling industry will be critical for Europe to maintain competitiveness with foreign markets and serve the booming need for batteries after 2030 or 2035.
What is driving battery recycling today
Raw materials are needed in the energy transition – most of which are currently sourced outside of Europe with an ever-increasingly scarce supply that is also subject to long lead times and dependency on geopolitical events. As a matter of fact, lack of access to raw materials could very well be the bottleneck for a successful energy transition. Hence, building European recycling capacity for batteries is a key part of the development of resilient supply chains to secure raw material and mitigate supply tensions. As such, it is critical that we explore the technologies, processes, and business models to bring these materials back into the loop for reuse in new batteries. At the same time, emerging battery recycling legislation is expected to push this market significantly in the coming years, asking for increasing recycled material content in new batteries being made. In addition, cell manufacturers and automotive OEMs are already taking active positions in the battery recycling markets: the high yields expected from recycling plants are a very attractive factor for these companies that want to mitigate their dependence on raw materials as much as possible. From a sustainability point of view, recycling end-of-life (EOL) batteries with the highest possible environmental standards is a must for cell manufacturing companies and also automotive OEMs’ ESG requirements. It will also give them a competitive advantage and increase customer acceptance. Not only is battery recycling more sustainable but it will bring additional revenue streams, create jobs, and foster economic growth.
State of play of battery recycling in Europe and beyond
Today, the recycling of lithium-ion batteries is still mainly based on small electronics such as laptops and mobile phones, as well as micromobility vehicles. In Europe, these batteries are currently collected as part of the traditional flow of batteries from appliances, making the volume of materials recovered through recycling relatively low. As the share of lithium-ion batteries increases in the overall flow, this percentage of recovery will increase dramatically: due to emerging supply constraints, metals included in the batteries will increase in value and therefore lead to more circular material flows. Traditionally, producers do not have interest in recycling beyond their legal responsibility, opting to fund recycling organisations to manage the waste. But this is because usually the recycling industry is not able to provide by-products that can be used in the original applications, only low value-added ones that are sold to other markets different from the ones they came from. This is not the case for the battery recycling industry. With state-of-the-art processes, by-products can be recovered at a rate of 80% or more and put back into a new battery. This is why producers are getting involved in recycling and will continue to even more.
With the expected massive global growth of EVs, the European market needs to ensure that the heart of the value chain migrates to and stays within Europe, reducing dependency on foreign producers. Taking into account that the great majority of lithium-ion batteries will be used in EVs, we do not expect a big flow of EOL batteries entering the stream in the next years as they most probably will have longer lifespans than we have previously thought. As such, while current recycling projects that are now coming online are critical for the battery future of Europe, for the next ten years or so it is expected that they will need to feed themselves from cell manufacturing scrap until EOL batteries from electric cars become the main inflow.
Seeing the potential, both established players and newcomers are trying to take market shares in this emerging industry. According to analysis conducted by the EBA250, there are over 35 lithium-ion battery recycling projects currently underway or in planning, with multiple projects coming online before 2025. These projects are pushing forward with both big and well-established companies such as Umicore, BASF, Nissan, and Volkswagen and newcomers installing pilots, such as Northvolt’s Revolt, Mecaware and Pure Battery Technologies. There is likewise a lot of development happening stateside with companies such as Redwood Materials and Li-Cycle also looking to expand to Europe. In Asia, where the battery recycling market is more mature, established players like SungEel in Korea and GEM in China have been involved in such projects for quite some time already.
The regulatory landscape
European regulation is poised to push for high recovery of materials and for the use of recovered materials into the production of new batteries. With the proposed EU Battery Regulation, legislation will support the existing drive to capture the most critical raw materials for the battery industry such as nickel, lithium, and cobalt through recycling while also addressing the CO2 footprint of batteries. Also included are battery labelling requirements and the EU’s proposed battery passport, which supports the sustainability of batteries through traceability and reporting. In the future, every battery in Europe will have a unique label with standard metrics recorded.
Whether we are looking at Europe, China or the US, battery regulation tries to foster this industry through various efficiency factors. In Europe it includes the concept of Recycling Efficiency – the weight percentage of the used battery that is recycled – the concept of Recovery Rate – the percentage of metal content that has to be recovered from the used battery – and the concept of Recycled Content – the percentage of metals in a new battery that has to come from a recycled origin. The ambition of the EU Battery Directive targets that 65% of a lithium-ion battery weight is recycled in 2025, increasing to 70% by 2030. For metals, a recovery rate of 90% for cobalt, nickel, and copper and 35% for lithium is targeted. By 2030 these targets raise to 95% and 70%, respectively. Based on the current projects coming online and in planning, we believe that these targets can be met through available technologies. If the demand for batteries continues to grow at today’s pace, the challenge will be that even when meeting recovery rates demanded for metals, the flows of recycled metals will not be enough to fulfil the requirements of recycled content in new batteries. In a way, this would be good news.
What are the technologies and business models we need to recycle batteries at-scale
There are two processes that can be used in battery recycling: pyrometallurgy and hydrometallurgy. Pyrometallurgy uses a robust and established process of high temperatures to recover materials using a blast furnace. Hydrometallurgy on the other hand is more complex, using chemical processes at low temperature, but it is the only current technology that can recover lithium. Therefore, as lithium-ion batteries flood the market, so are battery recycling technologies shifting to hydrometallurgy for the eventual large inflow.
While this technology is less mature, it has already been in place in Asia for a several years. In South Korea for example, it has proven to be very efficient in terms of material recovery of lithium, nickel, cobalt, and manganese, producing much lower CO2 emissions in the process.
These technologies are very sophisticated and might have a challenging ramp-up. But we believe that the market can accompany them to have a streamlined evolution of capacity. Today, recycling projects also try to capture cell manufacturing scrap as an important waste stream. This paves the way for partnerships between cell manufacturers and recyclers which will also play an instrumental role as the industry develops. Likely sometime around 2030, batteries from EVs are going to start entering the loop and opening up very interesting business models. First mainly fed by cell manufacturing scrap, then by used batteries, these projects offer the opportunity to make a smart ramp-up playing with the inflow mix.
Since the majority of the materials at the end of the recycling process can be fed back into battery production, and due to the extreme scarcity of these raw materials, the conditions for a closed-loop business model will be ripe. Here, producers don’t see recycling as a problem to be solved but rather as an opportunity: gain access to materials and make savings on them. Gigafactories will partner with recyclers to send them their cells and have them returned, as is already happening with Samsung in South Korea. There are quite a few initiatives worldwide in which gigafactories and OEMs are making all kinds of agreements, from commercial partnerships to joint ventures, often co-developing technology, with recycling companies, and even building their own recycling factories. And while there will be different business models, it is certain that the OEMs will take a strong position in the recycling industry in order to regain control of the batteries’ raw materials when the battery reaches the end of its life. This in turn will have positive implications on eco-design as well. In Europe, some projects are already starting this model with Daimler, BMW and Volkswagen in Germany working with technology providers. We also expect to see battery recycling increasingly brought in-house by the OEMs as part of their long-term strategies to build a closed loop on raw materials to ensure adequate supply.
Remaining challenges and outlook to 2035
Today, bolstered by initiatives like the EBA250, work is being done by the industry and we see great progress in that field. The battery recycling industry will thrive once we see larger volumes of lithium-ion batteries reach their end-of life and become available for recycling. But we also have other challenges to address in the coming decade. Hazardous waste classification of the intermediate product in the process – the black mass – and material handling, lack of standardisation on battery content and structure potentially presenting issues with recyclers, and lack of skilled people in the industry to name a few.
The many projects in the pipeline are promising, and we believe that raw material prices and pure scarcity, supported by regulation, will make battery recycling in Europe truly work at scale. Today’s market is very small compared to where we expect it to be five to ten years from now and we need to keep in mind that we are forecasting from very small figures with imprecise timelines. We are not completely sure about how many EVs are going to be sold ten years from now, or what the lifespan of the batteries in today’s EVs is – there is still some room for unexpected changes and new innovations. But, when the inflow of EOL batteries stabilises, be it in 2030 or 2035 or even further down the line, we strongly believe that the quantity of raw materials that are needed for EVs in Europe will mainly come from recycling and not from mining. It is a long way to go but the future potential for a European battery recycling industry is tremendous.
By Lluis Molina, EBA250 Business Development Manager, EIT InnoEnergy. Article originally published in Innovation News Network in November 2022.
Lluís Molina has a degree in Economics and a Master’s Degree by the University of Essex. He has more than 25 years of experience in the launch and development of new industrial projects, with an emphasis on CleanTech and Circular Economy. Today he is Responsible at the European Battery Alliance of the acceleration of strategic Raw Materials Extraction and Refining Projects.
More EBA250 news
Last week, the European Commission published the Clean Industrial Deal State Aid Framework (CISAF),…
We are pleased to welcome Emma Nehrenheim as new Managing Director of the European…
As Europe’s battery cell manufacturers face increasing competitive pressure, EBA250 remains actively engaged in…
InnoEnergy, the driving force behind the EBA250 initiative, introduces today its new brand identity,…
The new EU-funded facility will enhance global raw materials partnerships and access to Critical…
Last week, InnoEnergy and EBA250 represented the battery value chain in Brussels alongside Verkor…
ElevenEs, a European LFP lithium-ion battery manufacturer, has signed a Joint Development Agreement with…
The European battery industry has come a long way since the launch of the…
The 2024 Innovation Fund calls for proposals have been launched this week, with a…
Altris, a pioneering Swedish developer of sodium-ion battery technology, has reached significant milestones that…